Types of Molds: Open, Closed, Flexible, and Rigid Explained
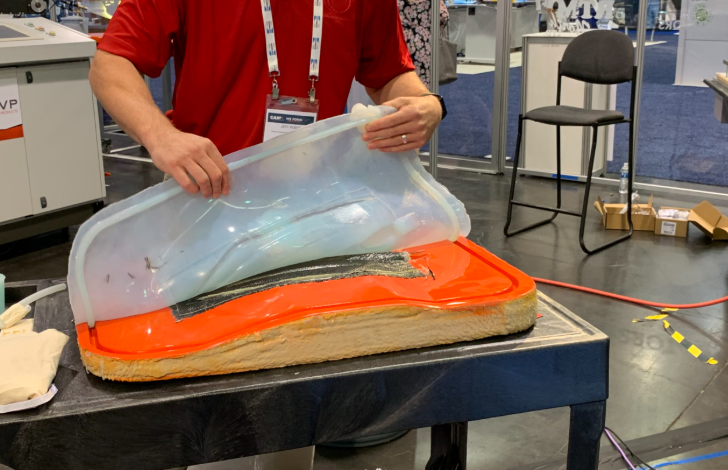
Choosing the right mold type is crucial for manufacturing success, impacting quality, cost, and timelines. This guide explores the four key mold types—open, closed, flexible, and rigid—along with their advantages, limitations, and applications to help you make the best choice for your production needs.
Understanding Open Molds
Open molds represent the simplest form of molding technology, featuring a single cavity that remains exposed to the atmosphere during the molding process. This straightforward design makes open molds ideal for basic shapes and applications where one surface doesn’t require a finished appearance.
Key Characteristics of Open Molds
Open molds operate on the principle of gravity or simple pressure application. Material is poured, pressed, or laid into the cavity, where it takes the shape of the mold’s interior surface. The exposed surface typically exhibits a different texture or finish compared to the molded surface.
Single-Surface Molding: Only one surface contacts the mold, creating a smooth finish on the molded side while the exposed surface may show texture variations or require secondary finishing.
Atmospheric Exposure: The open design allows for easy monitoring of the molding process but can lead to contamination or inconsistent surface quality on the exposed side.
Material Efficiency: Open molds typically use less material than closed systems since runners and gates are minimized or eliminated entirely.
Applications of Open Molds
Open molds excel in applications where cost-effectiveness and simplicity outweigh the need for precise surface finishing on all sides. Common applications include:
Fiberglass Components: Boat hulls, automotive body panels, and architectural elements frequently use open mold processes like hand lay-up or spray-up techniques, highlighting the versatility of fiberglass custom fabrication in creating durable and precise components.
Concrete Products: Decorative concrete panels, pavers, and precast elements often utilize open molds for cost-effective production.
Prototype Development: Open molds enable rapid prototyping with minimal tooling investment, allowing designers to test concepts quickly.
Art and Decorative Items: Sculptural elements, planters, and decorative panels benefit from the flexibility and low cost of open mold processes.
See also: Electric Vehicles: The Tech Behind the Shift
Advantages and Limitations
Open molds offer several compelling advantages. Low tooling costs make them accessible for small production runs or prototype development. Simple operation requires minimal training and equipment investment. Design flexibility allows for easy modifications and complex geometries that might be difficult in closed systems.
However, open molds also present certain limitations. Surface quality varies between the molded and exposed sides. Material waste can occur due to overfilling or trimming requirements. Process control is more challenging due to atmospheric exposure and manual operations.
Understanding Closed Molds
Closed molds feature two or more mold halves that completely enclose the molding cavity, creating a sealed environment for material processing. This design enables precise control over part geometry, surface finish, and material properties while supporting high-volume production requirements.
Key Characteristics of Closed Molds
Closed molds operate under controlled conditions with material injected, compressed, or transferred into the sealed cavity. The enclosed environment enables consistent processing conditions and superior surface quality on all part surfaces.
Complete Enclosure: All part surfaces contact mold surfaces, ensuring consistent finish quality and dimensional accuracy across the entire component.
Pressure Control: Sealed cavities enable precise pressure application, improving material flow and reducing defects like voids or incomplete filling.
Process Repeatability: Controlled environment conditions ensure consistent part quality from the first shot to the last, making closed molds ideal for high-volume production.
Closed Mold Processes
Several manufacturing processes utilize closed mold technology:
Injection Molding: Thermoplastic materials are heated and injected into closed molds under high pressure, creating precise parts with excellent surface finish.
Compression Molding: Thermosetting materials are placed in the mold cavity and compressed under heat and pressure until curing is complete.
Transfer Molding: Similar to compression molding but with material transferred from a separate chamber into the mold cavity through runners and gates.
Blow Molding: Hollow parts are formed by inflating heated plastic material against the mold walls using compressed air.
Applications of Closed Molds
Closed molds dominate high-volume manufacturing applications where consistency, precision, and quality are paramount:
Automotive Components: Interior panels, exterior trim, engine components, and electronic housings require the precision and repeatability of closed mold processes.
Consumer Electronics: Smartphone cases, laptop housings, and appliance components benefit from the tight tolerances and surface quality achievable with closed molds.
Medical Devices: Precision components, housings, and disposable items require the cleanliness and consistency of closed mold manufacturing.
Packaging: Bottles, containers, and caps are efficiently produced using closed mold processes that ensure consistent wall thickness and sealing properties.
Understanding Flexible Molds
Flexible molds utilize elastomeric materials like silicone, urethane, or rubber to create molds that can deform during part removal. This flexibility enables the production of parts with undercuts, complex geometries, and intricate details that would be impossible with rigid molds.
Key Characteristics of Flexible Molds
Flexible molds rely on material elasticity to accommodate complex part geometries. The mold material stretches and deforms during demolding, allowing parts with undercuts or complex shapes to be removed without damage.
Elastomeric Materials: Silicone rubber, polyurethane, and natural rubber provide the flexibility needed for complex part removal while maintaining dimensional stability during molding.
Undercut Accommodation: Complex geometries with undercuts, threads, and intricate details can be molded without the need for complex mechanical actions or multiple mold pieces.
Detail Reproduction: Flexible molds excel at capturing fine surface details, textures, and complex geometries that would be challenging for rigid molds.
Applications of Flexible Molds
Flexible molds shine in applications requiring complex geometries or small production volumes:
Prototyping: Rapid prototyping of complex parts benefits from the quick turnaround and geometric flexibility of flexible molds.
Art and Sculpture: Detailed reproductions of artistic works, figurines, and decorative objects utilize flexible molds to capture intricate details.
Medical Models: Anatomical models, prosthetics, and custom medical devices benefit from the precision and flexibility of elastomeric molds.
Specialty Components: Parts with complex internal passages, undercuts, or irregular shapes often require flexible mold solutions.
Advantages and Limitations
Flexible molds offer unique advantages for specific applications. Complex geometries can be molded without mechanical complications. Low tooling costs make them attractive for small production runs. Quick turnaround times enable rapid prototyping and design iteration.
However, flexible molds also have limitations. Lower durability compared to rigid molds limits their use in high-volume production. Dimensional stability can be challenging over extended production runs. Material compatibility may be limited depending on the elastomeric material used.
Understanding Rigid Molds
Rigid molds utilize hard materials like steel, aluminum, or engineered composites to create dimensionally stable tooling capable of withstanding high pressures and temperatures. These molds form the backbone of high-volume manufacturing across numerous industries.
Key Characteristics of Rigid Molds
Rigid molds provide the dimensional stability and durability required for high-volume production. The hard mold materials resist deformation under processing pressures while maintaining precise dimensions throughout extended production runs.
Material Durability: Steel, aluminum, and advanced composites provide the strength and wear resistance needed for high-volume production environments.
Dimensional Stability: Rigid materials maintain precise dimensions under processing conditions, ensuring consistent part quality throughout the mold’s service life.
Thermal Management: Rigid molds can incorporate sophisticated cooling systems to control processing temperatures and cycle times.
Rigid Mold Materials
Different materials offer specific advantages for rigid mold construction:
Tool Steel: Provides maximum durability and wear resistance for high-volume production but requires longer machining times and higher costs.
Aluminum: Offers excellent thermal conductivity and faster machining but with reduced durability compared to steel.
Beryllium Copper: Combines good thermal conductivity with reasonable durability, making it ideal for applications requiring rapid heat transfer.
Composite Materials: Advanced composites offer weight reduction and specific property advantages for specialized applications.
Applications of Rigid Molds
Rigid molds dominate high-volume manufacturing applications across multiple industries:
Automotive Production: Engine components, body panels, and interior parts require the durability and precision of rigid molds.
Aerospace Manufacturing: Critical components with tight tolerances and high-performance requirements utilize rigid mold technology.
Industrial Components: Gears, housings, and mechanical parts benefit from the dimensional stability and durability of rigid molds.
Consumer Goods: High-volume products like appliances, tools, and sporting goods rely on rigid molds for consistent quality and cost-effectiveness.
Comparative Analysis: Choosing the Right Mold Type
Selecting the appropriate mold type requires careful consideration of production requirements, part complexity, volume needs, and economic factors. Each mold type offers distinct advantages that align with specific manufacturing scenarios.
Production Volume Considerations
Low Volume Production: Open and flexible molds excel in low-volume applications where tooling costs must be minimized. The reduced complexity and material requirements make these options economically attractive for small production runs.
Medium Volume Production: Closed molds begin to show economic advantages as production volumes increase. The improved consistency and reduced labor requirements offset higher tooling costs.
High Volume Production: Rigid closed molds dominate high-volume applications where tooling costs are amortized over large production runs. The durability and consistency advantages become crucial for economic success.
Part Complexity Analysis
Simple Geometries: Open molds can handle simple shapes cost-effectively, while rigid molds provide better consistency for repeated production of simple parts.
Complex Geometries: Flexible molds excel at complex shapes with undercuts, while rigid molds with mechanical actions can handle complex parts in high-volume production.
Surface Requirements: Closed molds provide superior surface finish consistency, while open molds may require secondary finishing operations.
Economic Factors
Initial tooling costs vary significantly between mold types. Open molds require minimal investment, flexible molds involve moderate costs, while rigid closed molds represent substantial capital investment.
Production costs per part generally decrease with increased automation and consistency. Rigid molds enable lower labor costs and higher production rates, while flexible molds may require more manual intervention.
Lifecycle costs include maintenance, replacement, and quality considerations. Rigid molds typically offer longer service life and lower maintenance costs, while flexible molds may require periodic replacement.
Conclusion
Now that we have discussed the different types of molds and their application, it is clear that choosing the right type of mold greatly affects the overall production process and costs.